Transforming its Operations Through Digital Advancements
2005
GAMI Technology
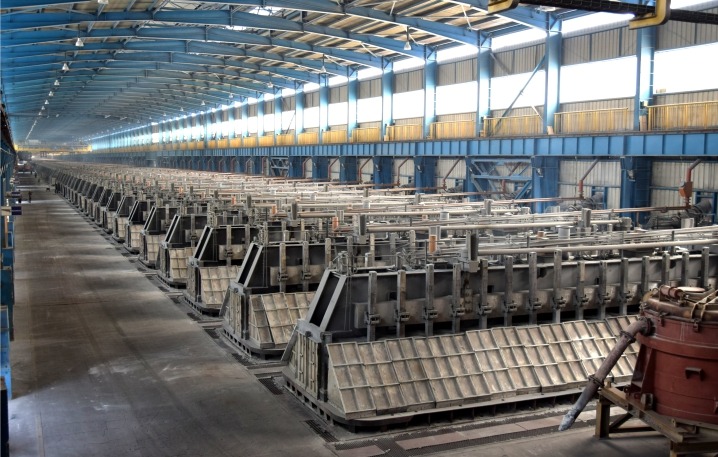

1975
Soderberg Technology
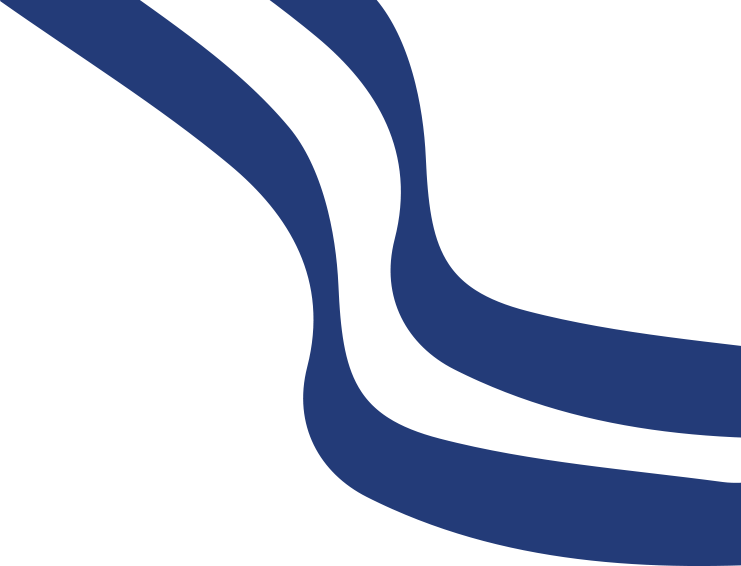
Tales of Leading Smelters
BALCO Innovates Aluminium Electrolysis with Start-Up Fuse Technology.
The invention relates to the aluminium production field using igneous electrolysis through the Hall-Héroult process. Alumina present in a fused bath is reduced to aluminium in reduction cells. These reduction cells are electrically connected in series operated at high amperage, through a system of busbars. Each cell is provided with an anode system and a cathode assembly. Within a series, the current enters a pot through the anode busbar.
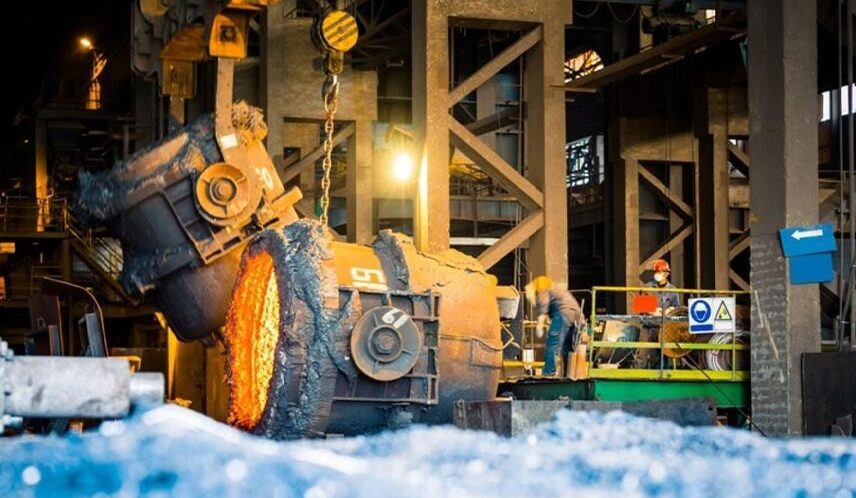
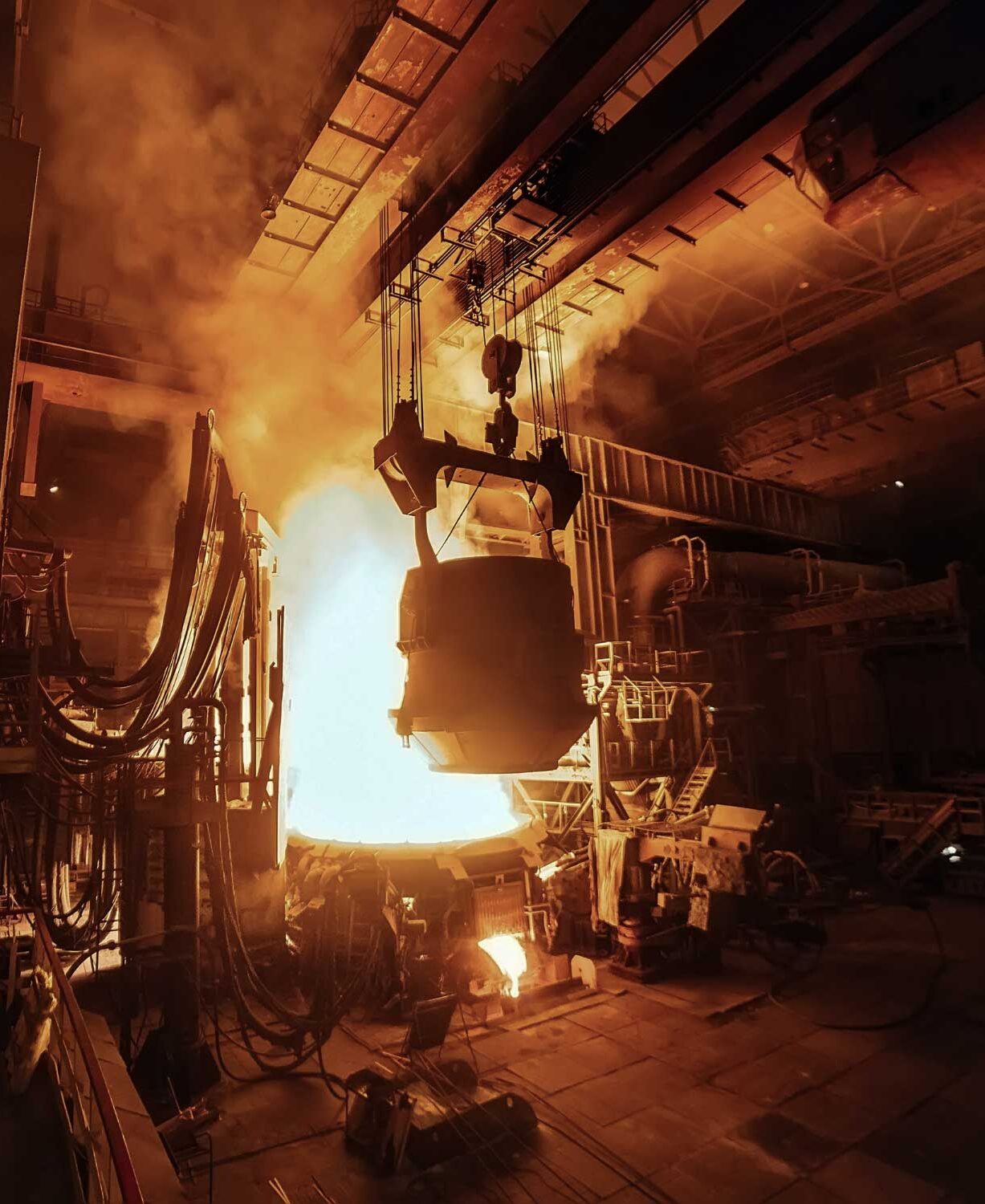
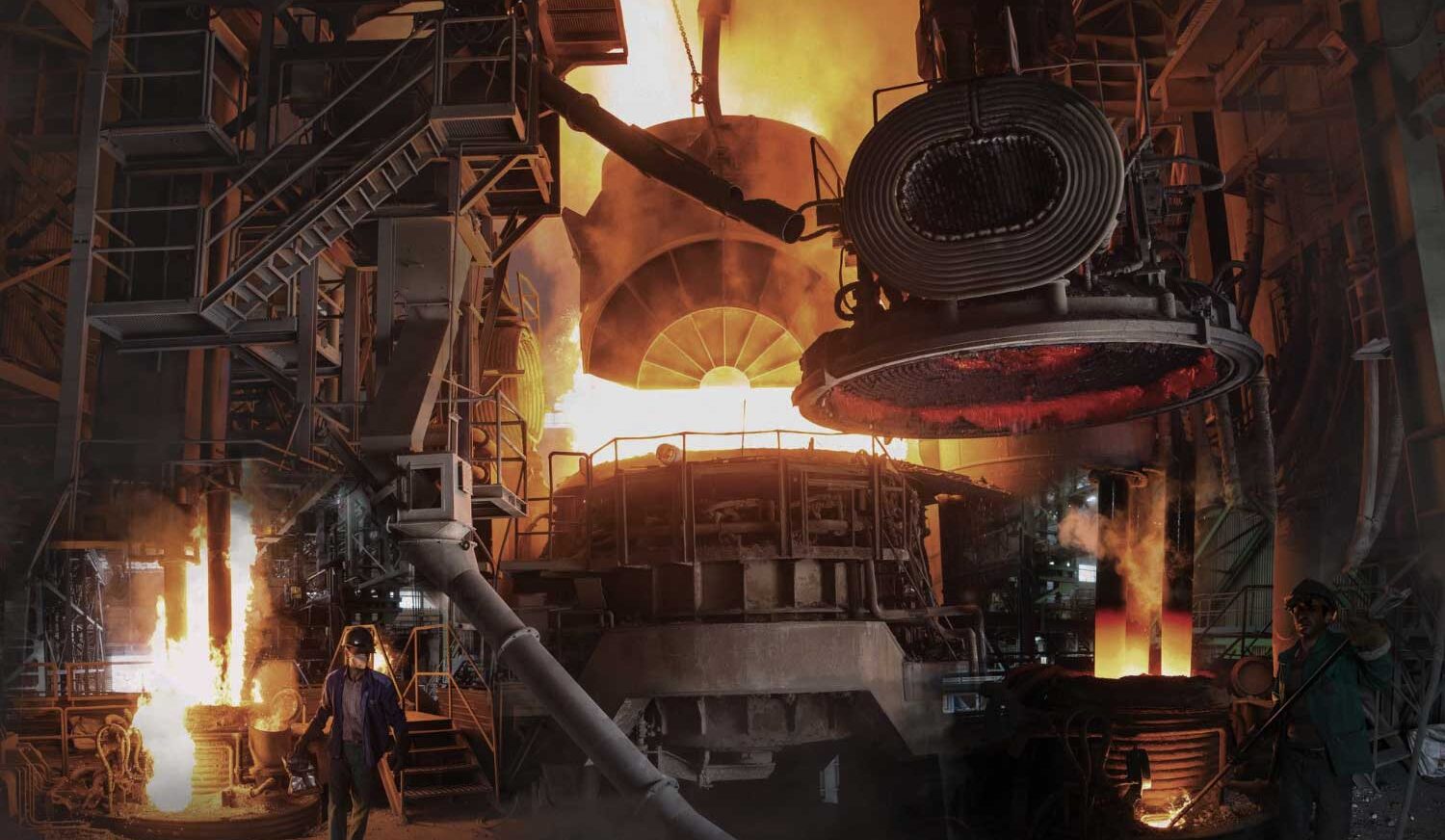
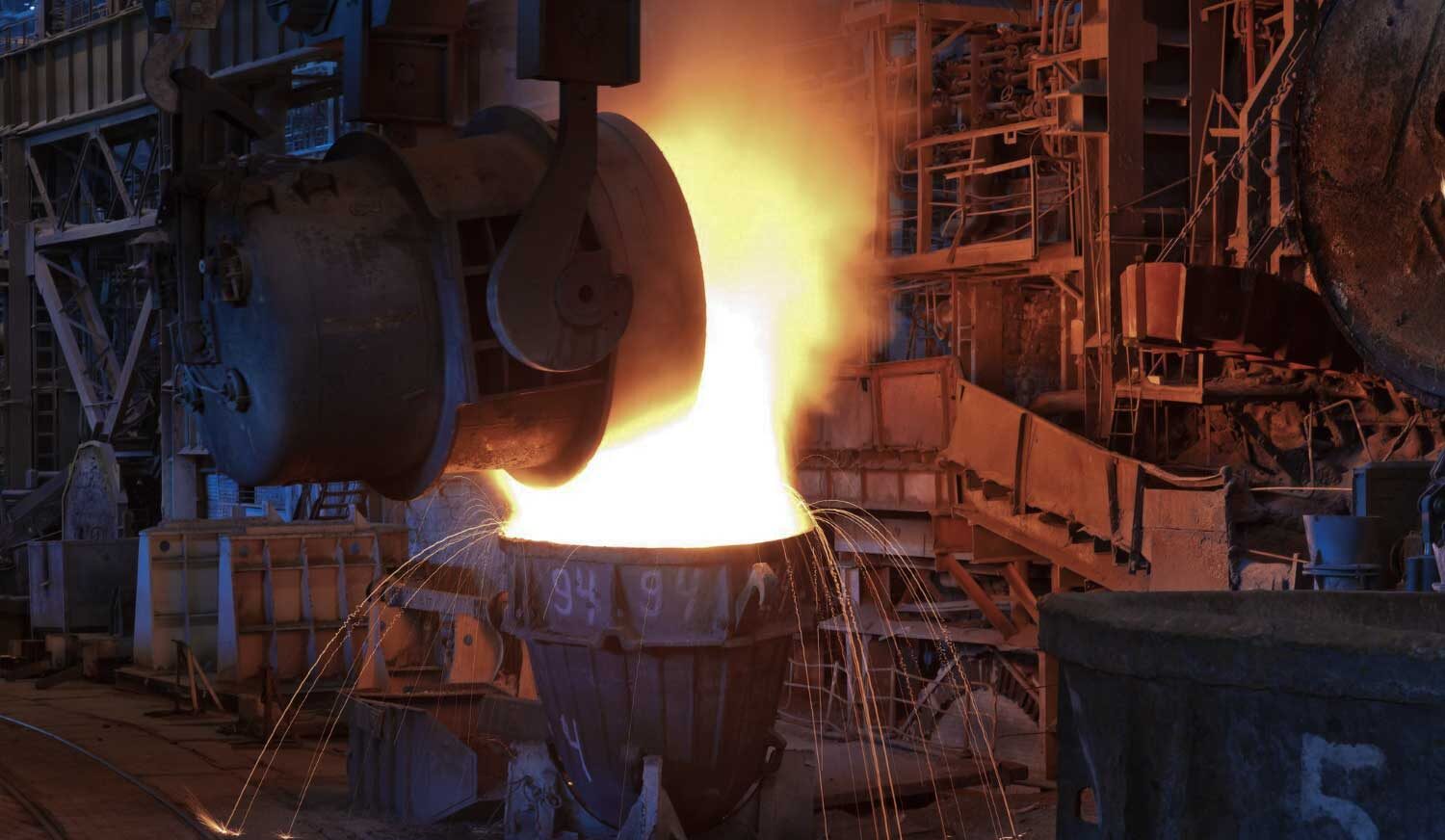
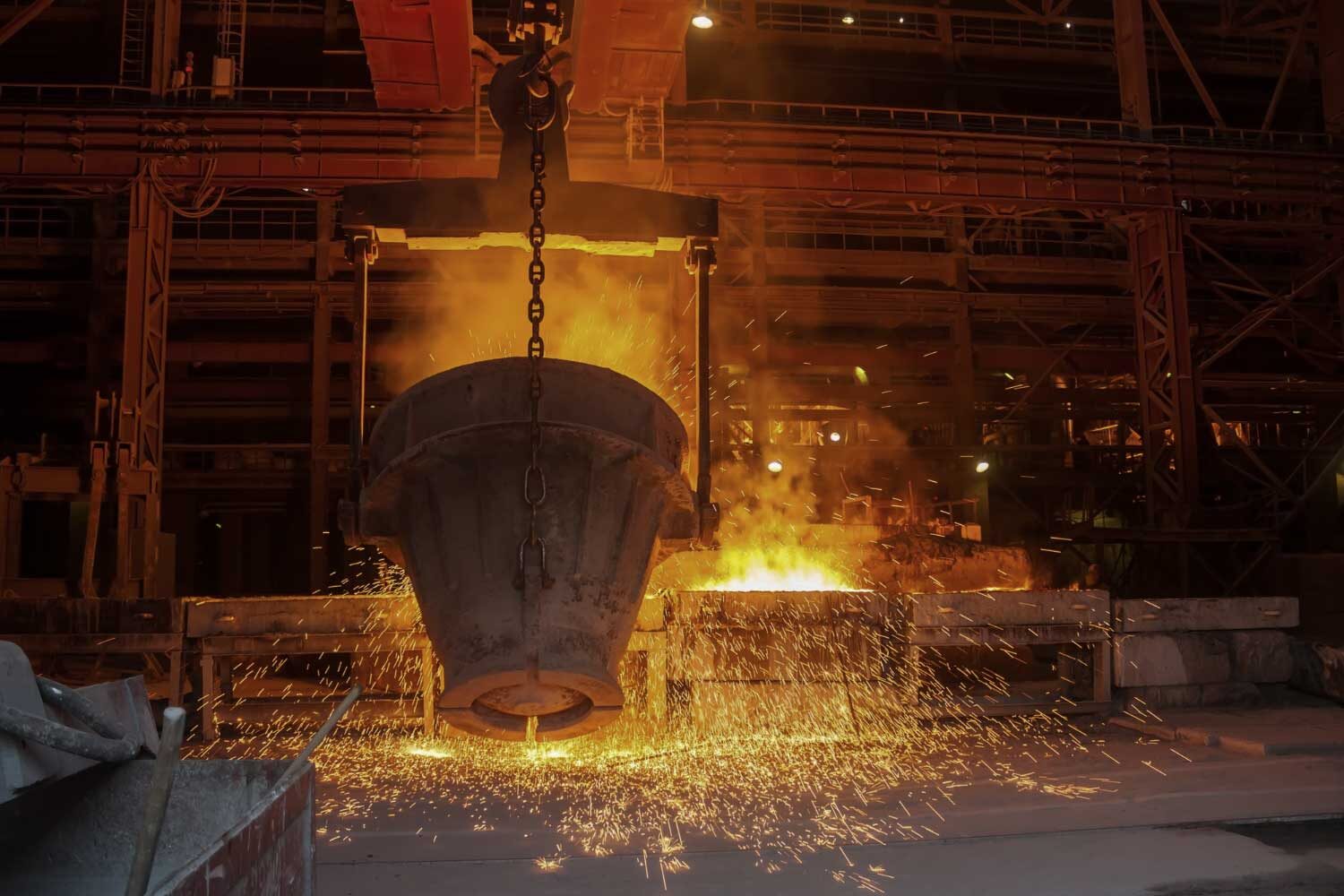